Innovative Applications of Thermoplastics in Modern Industries
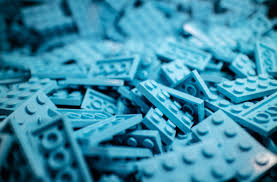
The Versatile World of Thermoplastics
Thermoplastics are a fascinating class of polymers that have revolutionised various industries with their versatility and practical applications. Unlike thermosetting plastics, which harden irreversibly upon curing, thermoplastics can be melted and reshaped multiple times without undergoing chemical changes.
Properties and Characteristics
One of the key characteristics of thermoplastics is their ability to soften when heated and harden when cooled, making them ideal for processes like injection moulding, extrusion, and thermoforming. They exhibit excellent toughness, flexibility, and chemical resistance, making them suitable for a wide range of applications.
Common Applications
Thermoplastics are used in diverse industries such as automotive, aerospace, packaging, electronics, healthcare, and construction. They are commonly found in products like plastic bottles, food containers, medical devices, car interiors, pipes, cables, and more.
Sustainability and Recyclability
With increasing focus on sustainability and environmental impact, thermoplastics offer an advantage as they can be recycled multiple times without significant degradation in quality. This recyclability factor makes them a preferred choice for eco-conscious consumers and industries striving to reduce their carbon footprint.
Advancements in Thermoplastic Technology
Ongoing research and development efforts continue to enhance the properties of thermoplastics through innovations such as reinforced composites, nano-additives for improved strength and performance, as well as bio-based alternatives derived from renewable sources.
Conclusion
Thermoplastics have undoubtedly transformed modern manufacturing processes by offering a sustainable and versatile solution for a wide array of products. As technology advances further, we can expect to see even more innovative applications of thermoplastics across various industries.
Essential Tips for Handling and Maintaining Thermoplastics
- Store thermoplastics in a cool, dry place to prevent degradation.
- Avoid exposing thermoplastics to high temperatures as they can soften or melt.
- Choose the right type of thermoplastic for your specific application to ensure optimal performance.
- Follow manufacturer’s guidelines for processing and shaping thermoplastics to achieve desired results.
- Consider recycling options for used thermoplastic materials to promote sustainability.
- Be cautious when handling molten thermoplastics to avoid burns or injuries.
- Regularly inspect thermoplastic components for signs of wear or damage and replace if necessary.
Store thermoplastics in a cool, dry place to prevent degradation.
It is essential to store thermoplastics in a cool, dry environment to prevent degradation and maintain their quality. Exposure to heat and moisture can lead to changes in the material properties of thermoplastics, affecting their performance and durability. By storing thermoplastics properly, you can prolong their lifespan and ensure that they remain in optimal condition for use in various applications.
Avoid exposing thermoplastics to high temperatures as they can soften or melt.
It is crucial to avoid subjecting thermoplastics to high temperatures as they have the tendency to soften or melt when exposed to excessive heat. This characteristic of thermoplastics highlights the importance of handling and storing them in environments with controlled temperatures to prevent any unwanted deformation or damage. By being mindful of temperature limitations, one can ensure the integrity and durability of thermoplastic materials in various applications.
Choose the right type of thermoplastic for your specific application to ensure optimal performance.
When working with thermoplastics, it is crucial to select the appropriate type of material that aligns with the requirements of your specific application. Choosing the right thermoplastic ensures optimal performance, durability, and functionality for the intended use. Factors such as temperature resistance, chemical compatibility, mechanical strength, and flexibility should be carefully considered to ensure that the thermoplastic material can meet the demands of the application effectively. By selecting the right type of thermoplastic, you can enhance performance and longevity while achieving desired results in your project or product.
Follow manufacturer’s guidelines for processing and shaping thermoplastics to achieve desired results.
It is crucial to adhere to the manufacturer’s guidelines when processing and shaping thermoplastics in order to achieve the desired results. Following these guidelines ensures that the material is handled correctly, leading to optimal performance and quality of the final product. By understanding and implementing the recommended processing techniques, such as heating temperatures, cooling rates, and moulding pressures, manufacturers can maximise the properties and characteristics of thermoplastics for their intended applications.
Consider recycling options for used thermoplastic materials to promote sustainability.
Consider exploring recycling options for used thermoplastic materials as a proactive step towards promoting sustainability. By choosing to recycle thermoplastics, you contribute to reducing waste and conserving valuable resources. Recycling these materials not only helps in minimising environmental impact but also supports the circular economy by giving new life to existing plastics. Embracing recycling practices for thermoplastics aligns with the growing global emphasis on sustainability and responsible resource management, making it a positive choice for a greener future.
Be cautious when handling molten thermoplastics to avoid burns or injuries.
It is crucial to exercise caution when dealing with molten thermoplastics to prevent burns or injuries. The high temperatures required to melt thermoplastics can pose a significant risk if proper safety measures are not followed. Always wear appropriate protective gear, such as heat-resistant gloves and goggles, when handling molten thermoplastics. Additionally, ensure that the work area is well-ventilated to avoid inhaling fumes. By prioritising safety precautions and handling procedures, the risk of accidents or injuries when working with molten thermoplastics can be greatly reduced.
Regularly inspect thermoplastic components for signs of wear or damage and replace if necessary.
Regularly inspecting thermoplastic components for signs of wear or damage is crucial to maintaining their functionality and ensuring safety. By conducting routine checks, any potential issues can be identified early on, allowing for timely replacements when necessary. This proactive approach not only helps in preventing unexpected failures but also extends the lifespan of thermoplastic components, ultimately contributing to the overall efficiency and reliability of the systems they are a part of.