Enhancing Road Safety with Hot Applied Thermoplastic Road Markings
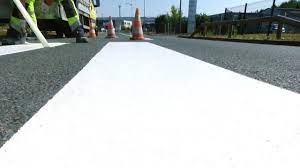
Hot Applied Thermoplastic Road Markings: Enhancing Safety and Durability on our Roads
Road markings play a crucial role in guiding and managing traffic flow, enhancing road safety, and improving overall road infrastructure. Among the various types of road markings available, hot applied thermoplastic road markings have gained popularity for their durability, visibility, and long-lasting performance.
Hot applied thermoplastic road markings are made from a mixture of synthetic resin binders, pigments, fillers, and glass beads. This mixture is heated to a high temperature until it becomes molten liquid form. It is then applied to the road surface using specialized equipment.
One of the key advantages of hot applied thermoplastic road markings is their exceptional durability. The material’s high melting point enables it to withstand heavy traffic loads, harsh weather conditions, and abrasive forces over an extended period. This makes it an ideal choice for roads with high traffic volume or areas where frequent maintenance may not be feasible.
The visibility of road markings is crucial for ensuring road safety. Hot applied thermoplastic road markings offer excellent retroreflectivity due to the incorporation of glass beads during the application process. These glass beads reflect light from vehicle headlights back to the driver’s eyes, making the markings highly visible even in low-light conditions or during nighttime driving. Enhanced visibility helps drivers stay within their lanes and follow traffic rules more effectively.
In addition to durability and visibility, hot applied thermoplastic road markings also provide skid resistance. The material’s textured surface helps improve tire grip on wet surfaces, reducing the risk of accidents caused by skidding or loss of control.
Another advantage of hot applied thermoplastic road markings is their quick drying time. Once applied to the road surface, they cool down rapidly and become solid within minutes. This allows roads to be reopened for traffic soon after application, minimizing disruption to motorists and ensuring smooth traffic flow.
Furthermore, hot applied thermoplastic road markings are environmentally friendly. The material is free from harmful solvents and heavy metals, making it a sustainable choice for road marking applications. It also has a longer lifespan compared to other types of road markings, reducing the need for frequent replacements and minimizing waste generation.
Hot applied thermoplastic road markings can be customized to meet specific road design requirements. They are available in various colours, widths, and designs, allowing for clear demarcation of lanes, pedestrian crossings, cycle paths, symbols, and other traffic control measures. This flexibility in design helps improve overall road aesthetics while maintaining functionality.
In conclusion, hot applied thermoplastic road markings offer numerous benefits that contribute to safer and more efficient roads. Their durability, visibility, skid resistance, quick drying time, and environmental friendliness make them an excellent choice for enhancing road infrastructure. By investing in hot applied thermoplastic road markings, authorities can ensure long-lasting performance and improve the overall safety of our roads for all users.
Frequently Asked Questions about Hot Applied Thermoplastic Road Markings in the UK
- What is the specification for thermoplastic road markings?
- What is hot applied thermoplastic road marking materials?
- What temperature should thermoplastic road marking be?
- How do you apply thermoplastic road markings?
What is the specification for thermoplastic road markings?
The specifications for thermoplastic road markings can vary depending on the specific requirements of a project and the regulations set by local authorities. However, here are some common specifications for thermoplastic road markings:
- Material Composition: Thermoplastic road markings are typically composed of synthetic resin binders, pigments, fillers, and glass beads. The exact composition may vary based on the desired characteristics of the markings.
- Thickness: The thickness of thermoplastic road markings is usually specified to ensure durability and visibility. It is typically in the range of 2-4 mm, although thicker applications may be required for heavy traffic areas or specific road conditions.
- Colour: Thermoplastic road markings are available in various colours to signify different types of lanes, symbols, or traffic control measures. Common colours include white, yellow, red, blue, green, and black.
- Retroreflectivity: Retroreflective properties are crucial for enhancing visibility at night or in low-light conditions. Thermoplastic road markings often incorporate glass beads to provide retroreflectivity by reflecting light from vehicle headlights back to the driver’s eyes.
- Skid Resistance: Skid resistance is an important characteristic to ensure vehicle tire grip on wet surfaces and prevent accidents caused by skidding. Texturing agents or aggregates may be added to thermoplastic materials to improve skid resistance.
- Drying Time: Thermoplastic road markings have a quick drying time compared to other types of road markings. They solidify within minutes after application, allowing roads to be reopened for traffic promptly.
- Application Method: Thermoplastic road markings are applied using specialized equipment that heats the material until it becomes molten liquid form and then applies it onto the road surface through extrusion or spray techniques.
- Adhesion: Proper adhesion between the thermoplastic material and the road surface is essential for longevity and durability. Adhesive primers or preheating of the road surface may be required to ensure strong adhesion.
- Longevity: Thermoplastic road markings are known for their durability and long-lasting performance. They are designed to withstand heavy traffic loads, harsh weather conditions, and abrasive forces for an extended period.
It’s important to note that these specifications may vary depending on local regulations, project requirements, and specific road conditions. Consulting with local authorities or experienced road marking professionals is recommended to ensure compliance with relevant standards and guidelines.
What is hot applied thermoplastic road marking materials?
Hot applied thermoplastic road marking materials are a type of road marking material made from a mixture of synthetic resin binders, pigments, fillers, and glass beads. This mixture is heated to a high temperature until it reaches a molten liquid form. It is then applied to the road surface using specialized equipment.
The key components of hot applied thermoplastic road marking materials include:
- Synthetic Resin Binders: These binders provide the adhesive properties necessary for the material to adhere to the road surface. They also contribute to the material’s durability and resistance to wear and tear.
- Pigments: Pigments are added to give colour to the road markings. Standard colours such as white and yellow are commonly used for lane markings, while other colours may be used for specific purposes such as red for bus lanes or blue for disabled parking bays.
- Fillers: Fillers are added to improve the material’s consistency and flow during application. They also help enhance the material’s skid resistance properties.
- Glass Beads: Glass beads are an essential component of hot applied thermoplastic road marking materials as they contribute to retroreflectivity. These tiny beads reflect light from vehicle headlights back towards the driver’s eyes, making the markings highly visible even in low-light conditions or at night.
Hot applied thermoplastic road marking materials offer several advantages over other types of road marking materials. They are known for their exceptional durability, visibility, skid resistance, quick drying time, and environmental friendliness. These characteristics make them a popular choice for enhancing safety and longevity on our roads.
What temperature should thermoplastic road marking be?
Thermoplastic road markings are typically applied at temperatures ranging from 180°C to 220°C (356°F to 428°F). The specific temperature requirements may vary depending on the manufacturer’s recommendations and the prevailing weather conditions during application. It is important to ensure that the thermoplastic material reaches its optimum melting point to achieve proper adhesion and durability on the road surface. Professional road marking contractors are trained to monitor and maintain the appropriate temperature throughout the application process to ensure quality results.
How do you apply thermoplastic road markings?
Applying thermoplastic road markings requires specialized equipment and a systematic approach. Here is a general overview of the process:
Surface Preparation: The road surface must be clean, dry, and free from any loose debris or contaminants. This ensures proper adhesion of the thermoplastic material.
Preheating: The thermoplastic material is heated in a preheater or melter to the recommended temperature specified by the manufacturer. This typically ranges from 180°C to 220°C.
Application Equipment: A specialized application machine, such as a screed box or extrusion machine, is used to apply the molten thermoplastic material onto the road surface.
Marking Layout: Marking lines and symbols are laid out on the road using chalk or masking tape to ensure accurate placement of the thermoplastic markings.
Application Process:
a) The application machine dispenses the heated thermoplastic material through a nozzle onto the road surface.
b) The material is spread evenly using a screed box or extrusion shoe that ensures consistent thickness and width.
c) Glass beads are immediately applied onto the freshly applied thermoplastic while it is still hot and sticky. These beads provide retroreflectivity for improved visibility.
d) For intricate designs or symbols, stencils may be used to guide the application process.
Cooling and Solidification: Once applied, the thermoplastic markings cool down and solidify within minutes due to their high melting point.
Traffic Control: To allow sufficient time for solidification, traffic should be diverted away from freshly applied markings until they have cooled completely.
It’s important to note that this process may vary slightly depending on specific equipment used, site conditions, and project requirements. It’s essential to follow manufacturer guidelines and industry best practices for optimal results.
Professional installation by experienced contractors with expertise in applying hot applied thermoplastic road markings is recommended to ensure proper application and adherence to safety standards.
Latest articles
- Plan Ahead: Essential M5 Closures Tonight for Maintenance Works
- Navigating the Challenges of Live Roadworks: Ensuring Safety and Efficiency on the Road
- Navigating Through M20 Roadworks: Tips for Drivers
- M25 Night Closures Scheduled for This Week: Plan Your Journeys Accordingly
- M25 Closures Scheduled for This Weekend: Plan Your Journey Ahead
Latest comments
Archive
- August 2025
- July 2025
- June 2025
- May 2025
- April 2025
- March 2025
- February 2025
- January 2025
- December 2024
- November 2024
- October 2024
- September 2024
- August 2024
- July 2024
- June 2024
- May 2024
- April 2024
- March 2024
- February 2024
- January 2024
- December 2023
- November 2023
- October 2023
- September 2023
- August 2023
- July 2023
- June 2023
- May 2023
- April 2023