Enhancing Road Safety and Durability with Cold Plastic Road Marking
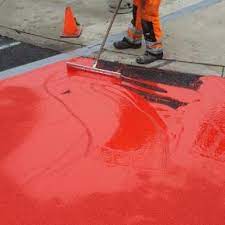
Cold Plastic Road Marking: Enhancing Safety and Durability on our Roads
Road markings play a crucial role in ensuring the safety and efficiency of our roads. They provide guidance to drivers, cyclists, and pedestrians, helping them navigate through traffic and understand the rules of the road. One popular method for creating durable and long-lasting road markings is cold plastic road marking.
Cold plastic road marking is a modern technique that has gained popularity due to its numerous advantages over traditional methods. It involves applying a specially formulated cold plastic material onto the road surface, which then hardens to create highly visible and durable markings.
One of the key benefits of cold plastic road marking is its longevity. The material used in this process is designed to withstand heavy traffic, harsh weather conditions, and regular wear and tear. Unlike traditional paint or thermoplastic markings that may fade or wear off over time, cold plastic road markings have a significantly longer lifespan.
Another advantage of cold plastic road marking is its superior visibility. The material used in this process contains reflective glass beads that enhance visibility during both day and night conditions. This ensures that road users can clearly see the markings even in low-light situations, improving overall safety on the roads.
Furthermore, cold plastic road marking offers excellent skid resistance. The textured surface created by this method helps vehicles maintain better traction, reducing the risk of accidents caused by skidding or sliding on wet or slippery surfaces. This makes it particularly beneficial for areas prone to heavy rainfall or icy conditions.
In addition to its durability and visibility, cold plastic road marking also offers environmental benefits. The materials used are non-toxic and do not contain harmful chemicals such as lead or solvents commonly found in traditional paint-based markings. This makes it a more environmentally friendly option for enhancing road safety.
Cold plastic road marking is also highly versatile. It can be used for various types of road markings including lines, arrows, symbols, pedestrian crossings, cycle lanes, and parking bays. Its flexibility allows for customization based on specific road requirements and local regulations.
When it comes to installation, cold plastic road marking requires professional expertise. Trained technicians apply the material using specialized equipment and techniques to ensure a precise and uniform application. This guarantees that the markings are clear, well-defined, and meet all necessary standards.
In conclusion, cold plastic road marking is a modern and effective method for enhancing safety and durability on our roads. Its longevity, superior visibility, skid resistance, environmental benefits, and versatility make it an excellent choice for road authorities and contractors. By investing in cold plastic road marking, we can create safer roads that improve traffic flow and reduce accidents, ultimately benefiting all road users.
7 Frequently Asked Questions about Cold Plastic Road Marking in the UK
- How long does cold plastic road marking take to apply?
- What is the best temperature to apply cold plastic road marking?
- How durable is cold plastic road marking?
- What are the advantages of using cold plastic road marking?
- Is cold plastic road marking suitable for all surfaces?
- Are there any health and safety considerations when applying cold plastic road marking?
- Can I use a spray gun or roller to apply cold plastic road markings?
How long does cold plastic road marking take to apply?
The time it takes to apply cold plastic road marking can vary depending on several factors, including the size and complexity of the project, weather conditions, and the experience of the application team. However, on average, the application process typically takes between 1 to 2 hours per marking.
Before applying cold plastic road marking, proper surface preparation is essential. This involves cleaning the road surface thoroughly to remove any dirt, debris, or existing markings. The surface may also need to be primed or leveled if required.
Once the surface is prepared, the cold plastic material is applied using specialized equipment such as hand-operated extrusion machines or spray guns. The material is carefully poured or sprayed onto the road surface in the desired shape and size for the markings.
After application, it usually takes a short amount of time for the cold plastic material to dry and harden. This can range from a few minutes to an hour, depending on various factors such as temperature and humidity. Once fully cured, which typically takes around 30 minutes to an hour, the road markings are ready for use.
It’s important to note that larger projects or those with complex designs may require more time for application and curing. Additionally, adverse weather conditions such as rain or extreme temperatures can affect the drying and curing process and may require adjustments to scheduling.
To ensure accurate timing estimates for your specific project, it’s recommended to consult with professional cold plastic road marking contractors who can assess your requirements and provide a more precise timeline based on their expertise.
What is the best temperature to apply cold plastic road marking?
The best temperature to apply cold plastic road marking typically ranges between 10°C (50°F) and 25°C (77°F). It is important to note that different manufacturers may have specific temperature recommendations for their products.
Applying cold plastic road marking in temperatures below the recommended range can negatively affect the curing process and result in reduced adhesion and durability. Similarly, applying it in extremely high temperatures can cause the material to dry too quickly, leading to poor bonding with the road surface.
To ensure optimal results, it is crucial to follow the manufacturer’s guidelines regarding temperature conditions during application. This will help ensure proper curing, adhesion, and longevity of the cold plastic road markings on our roads.
How durable is cold plastic road marking?
Cold plastic road marking is known for its exceptional durability. The material used in this process is specifically formulated to withstand heavy traffic, extreme weather conditions, and regular wear and tear.
Compared to traditional paint-based markings, cold plastic road markings have a significantly longer lifespan. They are designed to endure the constant pressure and friction caused by vehicles passing over them. This durability ensures that the markings remain clear and visible for an extended period, reducing the need for frequent maintenance or repainting.
The longevity of cold plastic road marking can vary depending on several factors such as the quality of materials used, traffic volume, climate conditions, and proper installation techniques. However, in general, cold plastic road markings can last anywhere from three to five years or even longer in optimal conditions.
The durability of cold plastic road marking is further enhanced by its resistance to fading caused by exposure to sunlight. The materials used in this process are UV-stable, meaning they can withstand prolonged sun exposure without losing their vibrant color or visibility.
Moreover, cold plastic road markings offer excellent resistance to chemicals and abrasion. They are less prone to damage from oil spills, harsh cleaning agents, or heavy scrubbing during maintenance activities. This resilience ensures that the markings maintain their integrity and visibility even in demanding environments.
It’s important to note that proper installation by trained professionals is crucial for maximizing the durability of cold plastic road marking. Skilled technicians ensure that the material is applied correctly with adequate thickness and adhesion to the road surface. This ensures a strong bond between the marking and the pavement, contributing to its long-lasting performance.
Overall, cold plastic road marking is renowned for its durability compared to other methods such as traditional paint or thermoplastic markings. Its ability to withstand heavy traffic, harsh weather conditions, UV exposure, chemicals, and abrasion makes it an excellent choice for creating long-lasting and highly visible road markings that enhance safety on our roads.
What are the advantages of using cold plastic road marking?
Cold plastic road marking offers several advantages over traditional methods, making it a popular choice for enhancing road safety. Here are some key advantages of using cold plastic road marking:
- Longevity: Cold plastic road markings have a significantly longer lifespan compared to traditional paint or thermoplastic markings. The material used is designed to withstand heavy traffic, harsh weather conditions, and regular wear and tear, ensuring durability and longevity.
- Visibility: The cold plastic material used in this process contains reflective glass beads that enhance visibility during both day and night conditions. This ensures that road users can clearly see the markings even in low-light situations, improving overall safety on the roads.
- Skid Resistance: Cold plastic road markings create a textured surface that provides excellent skid resistance. This helps vehicles maintain better traction, reducing the risk of accidents caused by skidding or sliding on wet or slippery surfaces. It is particularly beneficial for areas prone to heavy rainfall or icy conditions.
- Environmental Benefits: Cold plastic road marking materials are non-toxic and do not contain harmful chemicals such as lead or solvents commonly found in traditional paint-based markings. This makes it a more environmentally friendly option for enhancing road safety.
- Versatility: Cold plastic road marking can be used for various types of road markings including lines, arrows, symbols, pedestrian crossings, cycle lanes, and parking bays. Its flexibility allows for customization based on specific road requirements and local regulations.
- Professional Installation: Cold plastic road marking requires professional expertise during installation. Trained technicians apply the material using specialized equipment and techniques to ensure a precise and uniform application. This guarantees that the markings are clear, well-defined, and meet all necessary standards.
By considering these advantages, it becomes clear why cold plastic road marking is preferred by many authorities and contractors as a reliable solution for enhancing safety and durability on our roads.
Is cold plastic road marking suitable for all surfaces?
Cold plastic road marking is generally suitable for a wide range of surfaces. It can be applied to various types of road surfaces, including asphalt, concrete, and even brick or stone pavements. This versatility makes it a preferred choice for many road marking projects.
However, it is important to note that the condition and preparation of the surface play a crucial role in ensuring the effectiveness and longevity of cold plastic road markings. The surface should be clean, dry, and free from any loose debris or contaminants that could affect adhesion.
In some cases, additional surface preparation may be required, such as priming or repairing any cracks or potholes before applying the cold plastic material. This ensures proper bonding and adherence to the surface.
It is always recommended to consult with professionals or experienced contractors who specialize in road markings to assess the suitability of cold plastic road marking for specific surfaces. They can provide expert advice and guidance based on factors such as traffic volume, climate conditions, and the type of surface involved.
By considering these factors and working with knowledgeable experts, you can ensure that cold plastic road marking is applied correctly and effectively on suitable surfaces, maximizing its benefits in terms of safety and durability.
Are there any health and safety considerations when applying cold plastic road marking?
When applying cold plastic road marking, there are several health and safety considerations that need to be taken into account. These include:
- Personal Protective Equipment (PPE): It is essential for workers involved in the application process to wear appropriate PPE. This may include high-visibility clothing, gloves, safety goggles, and respiratory protection if required.
- Ventilation: Adequate ventilation should be ensured during the application process to prevent the build-up of fumes or vapours. Working in well-ventilated areas or using exhaust systems can help minimize exposure to potentially harmful substances.
- Material Handling: Cold plastic road marking materials should be handled with care, following the manufacturer’s instructions and any relevant safety data sheets (SDS). Workers should be trained on proper handling techniques to avoid spills or contact with skin.
- Fire Safety: Cold plastic road marking materials are typically flammable when in their liquid state. Therefore, it is important to follow fire safety protocols and avoid open flames or ignition sources near the working area.
- Slip and Trip Hazards: During the application process, there may be temporary changes in surface conditions that could increase the risk of slips and trips. It is important to maintain a clean and organized work area, use appropriate signage for temporary hazards, and ensure workers have proper footwear for traction.
- Traffic Management: Depending on the location of the road marking project, traffic management measures may need to be implemented to protect both workers and road users. This can include setting up barriers, signs, cones, or employing flaggers to direct traffic safely around the work zone.
- Training and Supervision: Workers involved in cold plastic road marking should receive adequate training on safe work practices, including handling equipment, using tools correctly, and understanding potential hazards associated with the process. Supervision is also crucial to ensure compliance with safety procedures.
It is important for companies undertaking cold plastic road marking projects to conduct risk assessments, develop safe work procedures, and adhere to relevant health and safety regulations. By prioritizing health and safety considerations, the risks associated with the application process can be minimized, ensuring the well-being of workers and the public.
Can I use a spray gun or roller to apply cold plastic road markings?
No, cold plastic road markings cannot be applied using a spray gun or roller. Cold plastic road marking requires specialized equipment and techniques for proper application. The material used in cold plastic road marking is a viscous liquid that needs to be heated to a specific temperature before it can be applied.
Typically, cold plastic road markings are applied using specialized machines that have built-in heating systems. These machines heat the cold plastic material to the required temperature and then apply it onto the road surface through nozzles or extrusion systems. This ensures precise and uniform application of the material.
The use of professional equipment is necessary to achieve the desired results in terms of durability, visibility, and skid resistance. Trained technicians who are experienced in working with cold plastic road marking materials should handle the application process to ensure proper installation and adherence to safety standards.
Using a spray gun or roller for cold plastic road marking may result in uneven application, reduced durability, and compromised visibility. It is important to follow industry best practices and use appropriate equipment for optimal results when applying cold plastic road markings.